Medical Molding Benefits from Revalidation of Injection Molding Processes Using Universal Set-up Data
by Bob Reese
RJG, Inc.
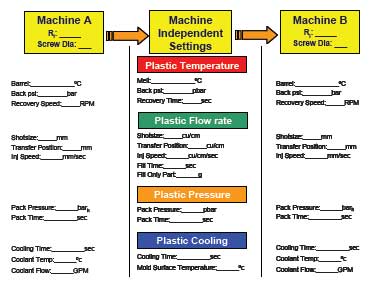
Figure 1: The machine independent set-up sheet (center) is used to duplicate the process on another press by matching the Four Plastics Variables.
In most injection molding applications, a mold is validated to run in a particular machine. Moving the mold to another press often is required for operational efficiency, but this usually requires revalidation. Depending on the application, revalidation can be very expensive. Costs include press time, material, engineering time, metrology and inspection, documentation and in the event of a failure, the costs of repeating the entire cycle.
When all these costs are taken into account, it is not unusual for a revalidation effort to exceed $10,000. In many cases, these costs can be dramatically reduced through the use of universal set-up data.
Traditional revalidation cycle
The traditional approach to revalidating a molding process closely follows the strategy for the initial process validation, and looks something like this:
Installation Qualification (IQ): In simple terms, demonstrating that the press and auxiliaries have been installed, calibrated and maintained properly
Operational Qualification (OQ): Here, a process is built on the new press, and process limits are defined. This often involves multiple trials and metrology. Designed Experiments frequently are used here (See the Design of Experiments article from the Fall 2012 issue of Plastics Business for more information). While the processing conditions from the original press are referenced, in many ways the process is rebuilt from scratch.
Performance Qualification (PQ): Parts are produced under normal production conditions to verify that the process consistently will produce acceptable product. A heightened level of part inspection generally is used to demonstrate part acceptability.
In the traditional revalidation cycle, the OQ and PQ both involve significant costs. It is important to note that parts from the PQ can be used for production once the revalidation is approved. However, if the revalidation fails, these parts must be scrapped, sorted or reworked, and the revalidation process starts over. This can add greatly to the cost of revalidation, making it even more important that steps be taken early to ensure success of the revalidation.
Revalidation using universal set-up data
Revalidation of the process using universal set-up data differs in two ways from the traditional revalidation. First, during the IQ, the suitability of the press for the given mold is analyzed. For example, the following traits should be assessed:
- The shot size should use 20 to 80 percent of the barrel's capacity to maintain control of shot size, fill speed and melt consistency.
- The clamp should be adjustable to within 10-20 percent of that required for the mold to ensure full clamping without crushing events.
- The mold should cover 2/3 of the distance between the tie bars to avoid excessive platen deflection.
- The injection unit should have enough fill speed to match the molds fill time requirement, and a first stage pressure greater than that required to fill the mold.
- Any material dryer should have appropriate residence time.
- The mold temperature controller should have sufficient volumetric flow to ensure adequate cooling.
By considering these factors as part of the IQ, the potential for successful transfer of the original process greatly is improved, and the risk of a costly revalidation failure is reduced.
Second, during the OQ, the original process is matched in terms of the Four Plastics Variables instead of trying to build a new process. The concept is simple yet powerful: if the melt temperature, flow rate into the mold, plastic pressure in the cavity and cooling rate are matched, the same part will be produced. This usually is much quicker and results in parts that more closely match the original process. Also, since the original process is matched, the need for a full OQ is eliminated. Instead, the original process can be duplicated and the original OQ can be utilized. This greatly reduces the time and cost of the revalidation.
Note that the PQ strategy is unchanged from the traditional revalidation. The PQ provides assurance the part quality remains consistent. Again, if the revalidated process is approved, the parts made during the PQ can be accepted, and the most significant cost becomes the additional inspection performed during this stage.
How it works: matching the four plastics variables
The core of this revalidation strategy revolves around matching the Four Plastics Variables on any press the mold runs in, and documenting the process in machine independent terms. The Four Plastics Variables are as follows:
Melt Temperature: This is the temperature of the melt as it's delivered from the injection unit into the mold. This can differ significantly from the barrel temperature settings. The best way to measure the melt temperature is with a melt probe inserted into a purge collected from a continuously running cycle. Newer low mass probes make this possible without preheating of the probe. Using the melt temperature from the original process, the barrel temperature settings on the new press can be adjusted to match the melt temperature.
Flow Rate: In its simplest terms, matching the flow rate means putting the same volume of material in the cavity in the same amount of time. The easiest way to match the flow rate from the original process is by matching the fill-only part weight and fill time. The fill-only part is created by turning off 2nd stage (hold) pressure. The resulting shot should generally be 95-98 percent full and should match the size and weight of the fill-only part from the documented process.
It can be useful to convert the linear shot size on the barrel to a volumetric measurement by multiplying it times the cross sectional area of the screw. This also can be done with linear injection speed to convert it to volumetric fill speed. This can be used to closely match volumetric shot size and fill speed between presses.
Plastic Pressure: After the cavity is full, it is pressurized to pack out the part. This is done during hold using 2nd stage pressure. While most molds do not have cavity pressure sensors to measure the exact pressure in the cavity, matching plastic pressure inside the barrel usually is sufficient. While most electric presses convert injection force directly into plastic pressure in the barrel, on hydraulic presses the plastic pressure must usually be converted from the hydraulic pressure.
The first step in converting hydraulic pressure to plastic pressure requires calculation of the intensification ratio. The intensification ratio is the area of the injection cylinder divided by the area of the screw. This then is multiplied times the hydraulic pressure to calculate plastic pressure in the barrel.
The second stage plastic pressure from the original process is calculated from the hydraulic hold pressure setting used on the original press. Next, the plastic pressure is converted to the hydraulic pressure to be used for the hold pressure on the new press. This can be repeated for back pressure as well.
Cooling Rate/Time: The cooling rate is controlled by the temperature of the mold surface. The mold surface temperature can be measured by breaking cycle during production and quickly taking surface temperature measurements using a surface temperature probe. The surface temperature can be taken on the original process and then matched on the new press.
The universal set-up sheet
The universal set-up sheet documents the process using the Four Plastics Variables (see figure 1 on previous page). Using this set-up sheet, the process can be duplicated on another press. The universal set-up sheet is created by converting the press settings from the original process into machine independent settings. Then the machine independent settings can be converted into settings to be used on another press. Because the process is being matched during the mold transfer, it is not necessary to perform a separate OQ when revalidating the process on another press. This saves considerable time and cost.
Normalize stroke and injection pressure data
Much of the information contained in the universal set-up sheet is contained in normalized stroke and injection pressure data. This data is read from a stroke sensor that measures the position of the screw during injection and from a hydraulic sensor that measures pressure in the injection cylinder. For electric presses, the data from the load cell on the screw is used.
Volumetric stroke data is calculated by multiplying the linear stroke data times the cross-sectional area of the screw. This is used to measure the volumetric flow rate and the total volume of material delivered during injection. Hydraulic pressure is multiplied times the intensification ratio to calculate plastic pressure. The types of information contained in normalized stroke and hydraulic data are shown in Figure 2. This can be used in place of the universal set-up sheet for many settings. However, melt temperature and cooling rate data still must be measured separately.
In addition to the universal set-up information, the normalized stroke and injection pressure data contains useful information about pressure response (the time it takes for 2nd stage pressure to reach a stable volume). The data can be used to detect problems like pressure limited filling or load sensitivity.
The role of in-cavity data
For most molds, the universal set-up sheet, along with normalized stroke and injection pressure data, are sufficient for duplicating a process on another press. However, for 10-20 percent of the most challenging molds, in-cavity data is needed to fully match the Four Plastics Variables and thereby match part quality.
Two types of sensors are useful for gathering in cavity data. The cavity pressure sensor provides precise information regarding pressure and flow rate, as well as indirect indication of melt temperature and cooling rate. The cavity temperature sensor provides precise information regarding mold temperature and flow rate, as well as indirect indication of melt temperature. The cavity temperature sensor provides very little information regarding pressure inside the mold. Matching in-cavity data provides the greatest assurance of producing identical parts when a mold is moved between presses.
Summary
A validation strategy based on universal set-up data and the Four Plastics Variables can greatly reduce the cost of revalidation and ensure more consistent part quality. These techniques have been used for years by some of the most respected device manufacturers in the world and have withstood the scrutiny of audits.