Close the Loop: Take Control of Water Efficiency
by Al Fosco
Frigel North America
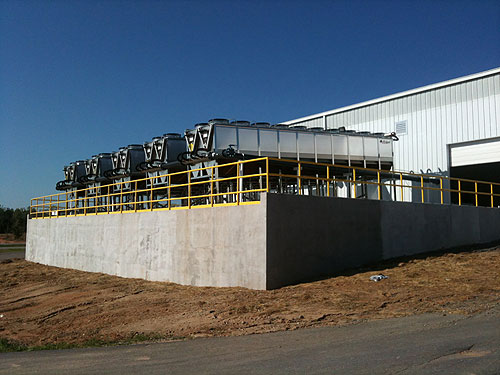
A closed-loop cooling system is a water- and energy-saving alternative to traditional cooling towers.
An effective cooling process is vital to production, and nothing is more critical to this process than its efficient use of water. This means utilizing the best auxiliary products and systems available to most cost-effectively control water use, reuse and waste. Mastering this capability not only will boost profitability, but, ecologically speaking, it also can greatly reduce water and energy waste, minimizing the use of chemicals during the process.
The closed-loop cooling process is gaining momentum throughout the industry because it works, providing effective water reduction solutions for plastics processors everywhere. This article reviews the benefits of closing the loop within a process cooling system and what to look for in a system.
Closed-loop systems: a refresher
A closed-loop process cooling system uses ambient air to cool process water. The technology is a water- and energy-saving alternative to traditional cooling towers, which many US companies use for process cooling.
The operation of closed-loop systems is straightforward. The system features a central cooler that provides clean water at the right temperature to processes year-round. It uses heat exchangers and an internationally patented adiabatic chamber to cool water circulated to it from process machines.
In the adiabatic chamber, a fine mist of water is pulsed into the incoming airstream during high ambient temperature conditions. The mist evaporates instantly, cooling the air before it impinges on the cooling coils that carry the process water. The process drops the temperature at or below the setpoint. Cooled water then is recirculated to a facility’s process machines. A microprocessor-based controller automatically maintains targeted cooling temperatures.
Efficiency advantages of closing the loop
The biggest and most obvious benefit of the closed loop? Resource efficiency – particularly in the form of water savings. A closed-loop system is an attractive alternative to cooling towers because it reuses water, often translating into water savings of up to 98 percent, which results in cost savings. A cooling tower, conversely, is an open-loop system that does not reuse water. The result is water waste in the form of evaporation.
Cooling tower systems leave the water exposed to outside elements, requiring costly chemical treatment and disposal. Closed-loop systems, however, minimize these issues and all of the related maintenance costs.
Adapting the system for climate
Instead of the "one-temperature-fits-all" approach of a typical cooling tower/central chiller system, the closed-loop system can be configured to provide precise process water at each machine by pairing with machine-side chillers. This configuration not only improves part quality and cycle time, but also saves energy overall because the entire system can maintain a water temperature that’s higher than required at individual machines.
This capability is just one way the closed-loop system is more flexible in terms of energy use than a traditional cooling system. In fact, the system’s central cooler offers four different stages with varying levels of energy use, depending on ambient conditions and setpoint requirements.
- Dry cooling. In moderate temperatures, the central cooler continuously routes water returning from the process through heat exchangers. Exhaust fans at the top of the central cooler ensure a steady stream of incoming cool air and outgoing heated air. The heat exchangers and exhaust fans together are all that’s needed to cool process water.
- Adiabatic cooling. This function only activates in hot weather as needed to meet cooling needs.
- Increased adiabatic cooling. A patent-pending "adiabatic booster system" enables the unit to deliver even lower process cooling water temperatures in the hottest climates, still without the use of central chiller.
- "Free cooling." The system automatically shuts down any chillers and lets the central cooler provide all the cool process water needed via ambient air flow.
Taken together, these capabilities mean that a closed-loop adiabatic process cooling system can reduce energy consumption for process cooling by as much as 50 percent as compared to a conventional cooling tower/central chiller system.
System design 101
A range of factors influences the design of a closed-loop system and its performance. When planning, consider the following:
- System sizing. It requires an analysis of the cooling load required, as well as the process temperature to be maintained. A rule of thumb is for the system to provide 20 percent to 30 percent more capacity than needed. The calculation also should account for unclean cooling water because it can limit system performance.
- Plant location. System performance is dependent on ambient conditions. All things being equal, a system in New Orleans typically will call for more cooling capacity than a system in Chicago.
- Future plans. Whether a plant expansion is imminent or a remote possibility, the system design should support the potential need for more cooling capacity down the road.
- Available footprint. Even though it can be located on the roof or the side of the facility, consider available space for the system. Also account for acceptable noise levels and other details, such as requirements for UL-listed electrical panels.
Equipment considerations
As the popularity of closed-loop systems grows, so does the number of equipment choices. A checklist of key considerations should include the following:
Modularity of auxiliary components. Some systems require more time to expand due to the need to connect manifolds, reservoirs and piping in the field, whereas a self-contained modular system expedites installation. Also eliminated with a modular "package" is the need to drain water from the system. The net result is less worry about plant downtime during an upgrade or expansion.
Cooling in unique conditions. Systems differ in how they cool process water in the hottest climates when high ambient temperatures routinely prevent water from reaching 90-95 degrees F (32-35 degrees C), or in situations when the application requires water temperature in the 85 degrees F range (30 degrees C). Some systems spray extra water directly on the heat exchanger, which can lead to exchanger pitting and premature maintenance. Conversely, a system that temporarily floods heat exchanger surfaces and also drains (and reuses) the excess water reduces the potential for pitting for system longevity.
Friendliness of programmable controls. The microprocessor-based control should be intuitive since it controls all functions. They also make it easier to optimize system performance and plan for routine maintenance. Check to see if the supplier provides remote Internet monitoring services if a higher level of support is the goal.
Use of protective materials. The materials used to construct system components vary by supplier. The shell of a central cooler, for example, might be built with galvanized steel, which doesn’t provide the same level of protection against the elements as stainless steel. Or, the heat exchangers might call for a more-resistive acrylic coating (standard on some brands) for use in harsh environments. Understanding the options and investing in protective materials often saves in the long run.
Functionality in tight spaces. A system might need to fit in a tight space, which is fine as long as airflow is unrestricted. Ensure the system is available with space-saving options such as roof panels that allow multiple central cooling units to be positioned more closely together. Another example is extended legs that support the cooler to provide ample airflow in smaller confines, sometimes even side-by-side.
Putting the needs of the operation first
Closed-loop cooling is a great way for plastics processors to enhance processes and achieve cost and resource efficiency. Selecting the right closed-loop process cooling system for a new or existing facility requires careful planning, expert advice and support. Partner with a proven supplier that not only has experience with cooling technologies, but also understands both the manufacturing processes involved and the overall goals of the operation.